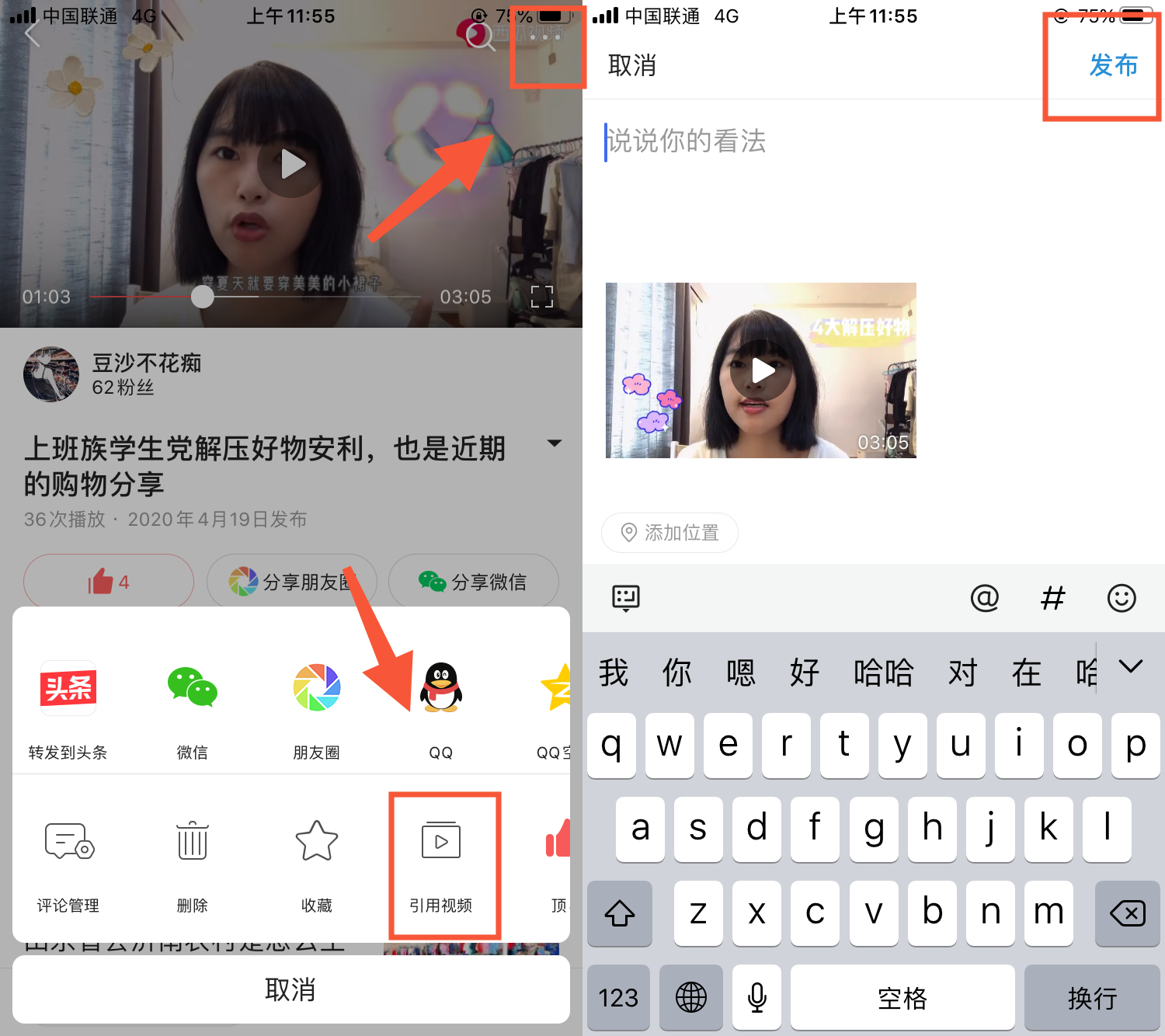
Essential Guide to Product Production Methods
In today's competitive landscape, effective product production methods play a vital role in manufacturing success. Companies must choose strategies that balance efficiency, cost, and quality to meet market demands. Understanding various production techniques can significantly impact a company's overall productivity and profitability.
This article explores manufacturing processes, production planning strategies, and product development techniques essential for contemporary manufacturers. We'll delve into topics like automation versus manual labor and the importance of sustainable production methods. Here are the key takeaways you can expect:
- Insights into assembly line production versus batch production.
- Strategies for production optimization and cost-effective manufacturing.
- Best practices for quality control and project management in production.
Choosing the Right Manufacturing Processes
When deciding on manufacturing processes, businesses need to assess the most suitable production method for their product lifecycle. Factors like market demand forecasting and technology integration in production are key components influencing these decisions.
Assessing Production Efficiency Improvement
Improving production efficiency involves analyzing workflow and implementing lean manufacturing principles. Organizations often utilize tools such as performance benchmarking to identify bottlenecks and areas for improvement. By assessing efficiency metrics in production, businesses can make informed decisions regarding resource allocation, ultimately maximizing output.
Understanding Cost-effective Production
Cost analysis in production is essential for maximizing profitability. Companies must explore machinery selection for production that balances initial investment with long-term returns. This includes evaluating batch production techniques that may offer lower setup costs compared to high-volume assembly line production.
Technology in Production
The role of manufacturing technology trends cannot be overstated. Automation and advanced machinery can significantly enhance production capabilities. Adopting just-in-time manufacturing techniques can help align production schedules with market demand, minimizing waste and optimizing inventory management systems.
Implementing Successful Project Management in Production
Establishing a robust project management framework is crucial for effective manufacturing. Successful product production relies on structured approaches such as production scheduling and resource allocation in production.
Production Scheduling Strategies
Utilizing agile production methodologies allows companies to adapt to market changes rapidly. An effective production scheduling strategy ensures that manufacturers can respond to fluctuating customer demands without compromising quality or efficiency. Integrating technology and automation in this phase can further streamline operations.
Quality Control in Manufacturing
Implementing strict quality assurance processes is vital for maintaining production standards. Regular production audits and quality metrics enable businesses to identify defects early in the manufacturing process. This proactive approach not only enhances product reliability but also aids in defect reduction strategies.
Employee Engagement in Production
Workforce management in manufacturing goes beyond just assigning tasks. Engaging employees through training and development fosters a culture of continuous improvement. High employee engagement can lead to increased productivity and elevated quality outcomes across the entire production line.
Evaluating Production Risks and Compliance Standards
Assessing production risks is essential for maintaining operational integrity. Manufacturers must regularly review compliance standards to ensure adherence to regulations, thus safeguarding their business against potential legal challenges.
Sustainable Production Methods
Adopting sustainable production methods not only minimizes environmental impact but can also improve a company's public image and market appeal. By utilizing raw material procurement strategies focused on sustainability, businesses can contribute positively to their community while optimizing costs.
Market Demand Forecasting Techniques
Effective market analysis for production helps align resources with consumer needs. Utilizing data-driven decision-making techniques enables businesses to accurately predict market trends and adjust production strategies accordingly. This adaptability is crucial to maintaining a competitive advantage in a fast-paced market.
Feedback Loops in Production
Incorporating feedback loops in production enhances customer-driven production methodologies. By understanding consumer preferences and integrating customer feedback, manufacturers can tailor their products to meet specific demands, ultimately leading to greater satisfaction and loyalty.
Integrating Innovation in Product Development
Product lifecycle management is fundamental for keeping pace with industry innovation. Manufacturers must continually revise their product development techniques to remain competitive.
Prototyping and Product Testing Methods
Utilizing prototyping for product development allows manufacturers to test concepts rapidly. Advanced product testing methods ensure that products meet customer expectations and industry standards before launch. By employing thorough testing and quality assurance processes, companies can significantly reduce time-to-market.
Competitive Production Analysis
Investing time in competitive production analysis enables businesses to assess their processes against industry leaders. By understanding best practices in production, such as automation strategies and effective workflow analysis in manufacturing, organizations can identify areas for improvement and seize opportunities for advancement.
Implementing Resource Allocation Models
Resource allocation in production is a balancing act. Implementing capacity planning models helps ensure optimal utilization of resources, minimizing waste while maximizing output. Companies must assess production capacity to align with market needs efficiently.
Common Challenges and Best Practices in Manufacturing
Manufacturers face various challenges during the product production process; understanding and addressing these issues is critical for success. Companies can adopt proven best practices to mitigate common production risks.
Defect Reduction Strategies
Implementing defect reduction strategies is essential to maintain product quality. Quality metrics must be adhered to at every stage of production. Investing in employee training and robust quality assurance processes can significantly reduce error rates.
Inventory Control Methods
Effective inventory management systems ensure a balance between supply and demand. By leveraging technology trends in inventory control, businesses can enhance their production efficiency. Automated tracking and just-in-time systems help prevent excess inventory, reducing costs and improving cash flow.
Technological Innovations in Production
Staying ahead of technological innovations in production helps businesses maintain a competitive edge. Companies must continuously evaluate and integrate new technologies that enhance production capabilities or improve operational efficiencies, while also considering sustainable production practices.
Conclusion: The Value of Strategic Production Planning
In conclusion, effective product production methods encompass a strategic approach to manufacturing that integrates technology, workforce management, and adherence to quality standards. By focusing on production optimization strategies and embracing innovation, businesses can improve their operational performance and remain agile in a changing marketplace. Adapting to consumer needs and foreseeing market trends are pivotal to sustaining growth and achieving long-term success.
By considering different manufacturing processes and meticulously planning each aspect of production, manufacturers can optimize their resources while maximizing product quality and customer satisfaction.